Criteria for the selection and design of rolling bearings
As one of the most widely used components in the world, rolling bearings have long been considered fairly simple to select. Typically, engineers would only specify the axial and radial forces acting on them, and clever product configurators would deliver the appropriate rolling bearing to match.
- Running accuracy,
- Running smoothness,
- Stiffness,
- Durability and
- Heat generation
however, the precise selection of the right rolling bearing is becoming increasingly difficult.
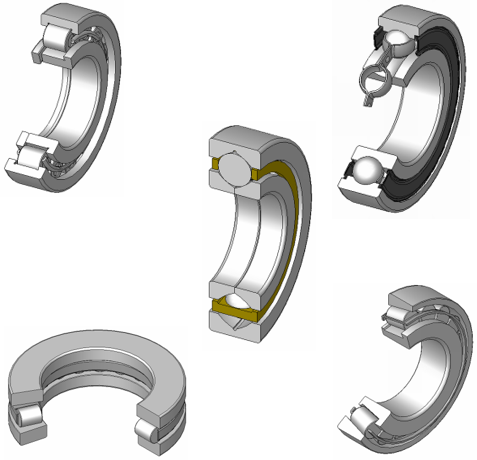
Above all, the influence of the surrounding components and assemblies can be significant in many cases. And this can only be partially taken into account by the rolling bearing supplier when the bearing is selected.
As a result, the actual operating point (combination of all loads) of the bearings in the assembly cannot be estimated simply by experience.
Simulation of rolling bearings
Simulation has the potential to revolutionize the development of engineering products in all industries and fields. Especially the Finite Element Analysis (FEA) offers many possibilities here due to its generality.
However, to date, finite element simulation of rolling bearings has left a lot to be desired by industrial companies. The reason is that the classical models:
- Either oversimplified (and therefore not very meaningful).
- or too detailed (and therefore associated with enormous computational effort) could be modeled.
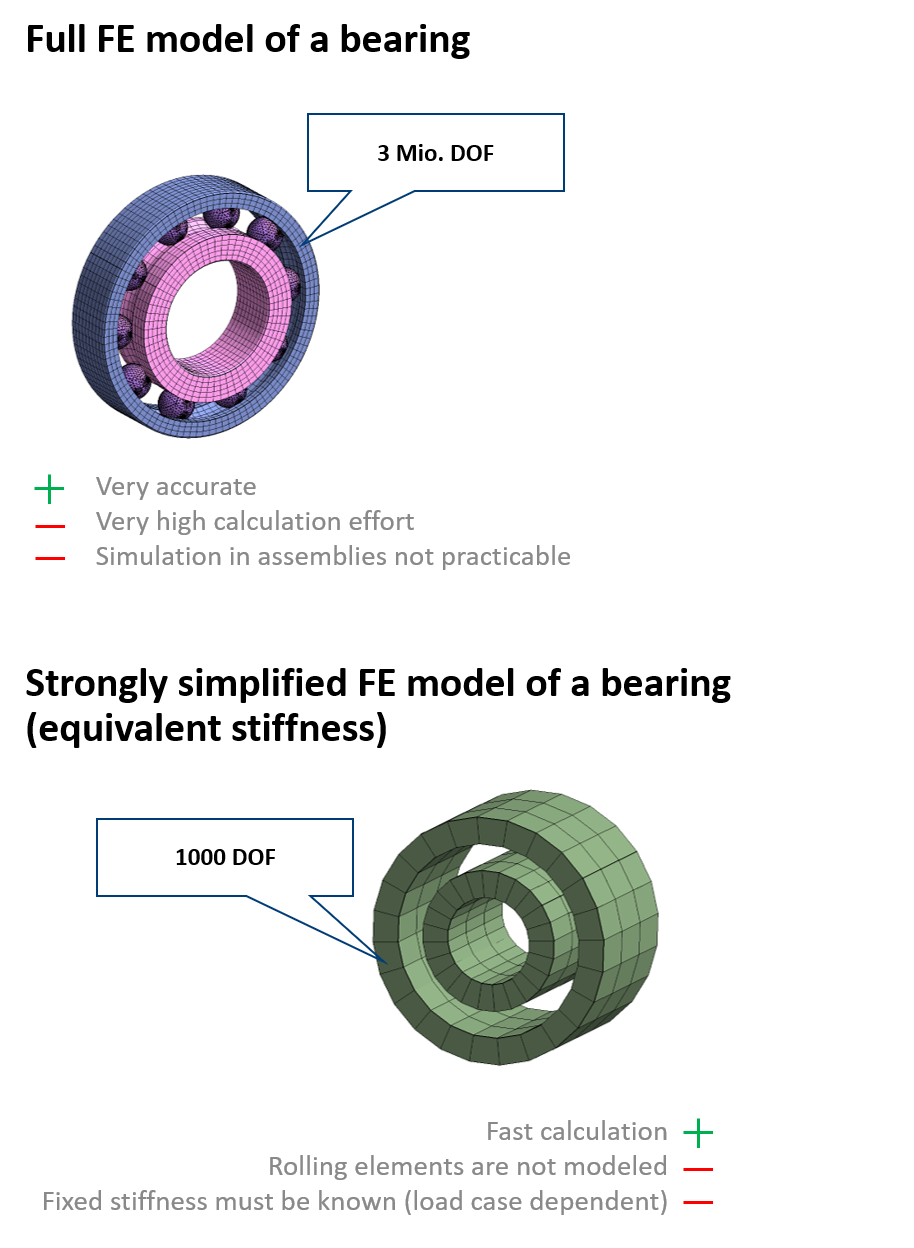
One of the goals at Meshparts, therefore, was to develop efficient (accurate and fast-calculating) rolling bearing models that could function seamlessly in entire FE assemblies.
After many years of work in this area, we have developed and refined a modeling style that combines the advantages of both previous model types.
High-detail models of rolling bearings
Meshparts' high-detail rolling bearing models are FE hybrid models: The bearing rings are elastic solids, while the ball and roller models are modeled using nonlinear equivalent springs. As a result, the bearing models have virtually no effect on the model size. Despite highly detailed bearing models, the simulation times are comparable to the classical, highly simplified bearing models.
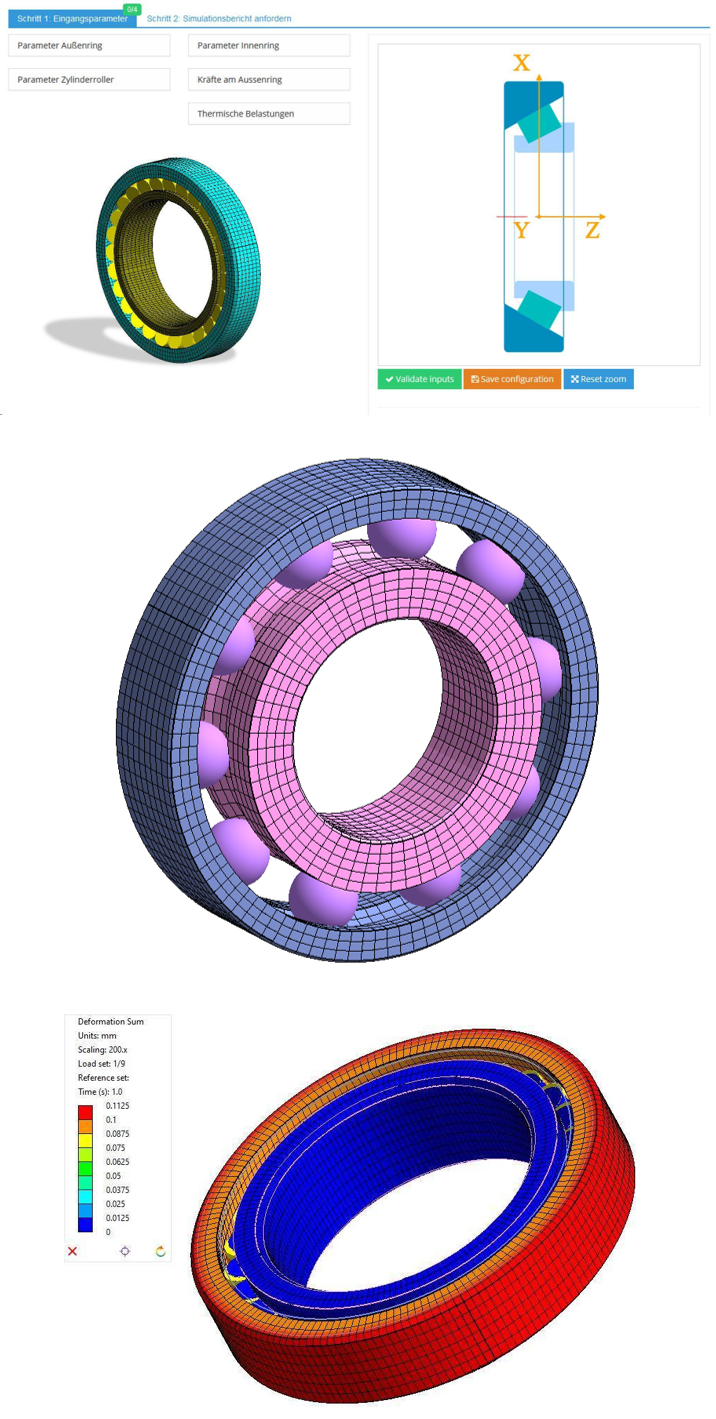
The nonlinear spring characteristic of the spherical models is determined according to Hertzian theory. Multiple spring models are used for the cylindrical and tapered rollers, since these rolling elements are divided mentally into several disks. Each disk is modeled by its own nonlinear spring stiffness. By having enough individual spring elements (cylindrical disks), not only the varying diameter of tapered rollers but also the crowning of the rolling elements can be taken into account.
From the above, it can be deduced that our high-detail rolling bearing models do not require specification of bearing stiffness. Instead, the models are configured by specifying geometric dimensions. For example, ball or roller diameter, number of rolling elements and osculation are required. The osculation can usually be estimated as 0.52. Common bearing types (deep groove ball bearings, angular contact ball bearings, cylindrical roller bearings, tapered roller bearings, etc.) can be quickly parameterized using our simulation apps. Afterwards, the bearing configurations are simply copied/pasted into our FE software. High-detail models for FE analysis are then created at the push of a button.
Realistic behavior of simulation models
Meshparts' high-detail rolling bearings simulation models behave realistically:
- As the load increases, the contact angles of the balls grow. The operating point-dependent bearing stiffness is thus only determined during the simulation.
- For balls as well as for cylindrical and tapered rollers, clearance can be defined parametrically.
- Installation conditions such as interference fit and bearing preload are implicitly considered because the bearings are part of larger FE assemblies.
- Thermal loads resulting in expansions of bearing rings, bearing housings and shafts automatically affect the calculated bearing load and bearing operating point.
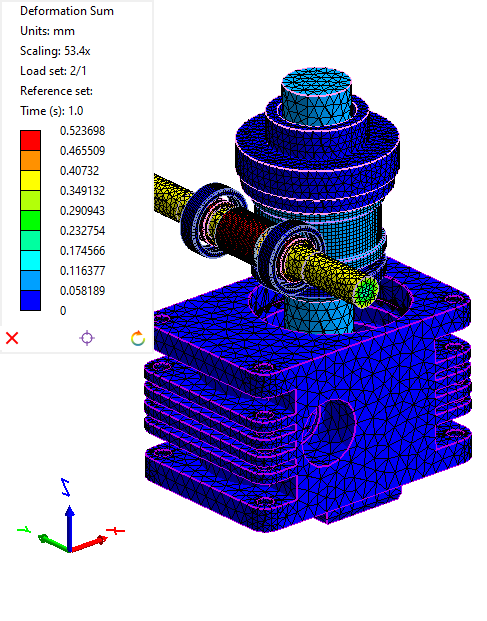
Rolling bearings simulation software
Our software related to rolling bearing model library is installed locally. You have the possibility to calculate any number of design variants of rolling bearings. The software is available as an annual or monthly subscription. We provide standard support (max. 8 hours per year) or intensive maintenance and support (8 hours per month). In addition, we recommend a one-day training.
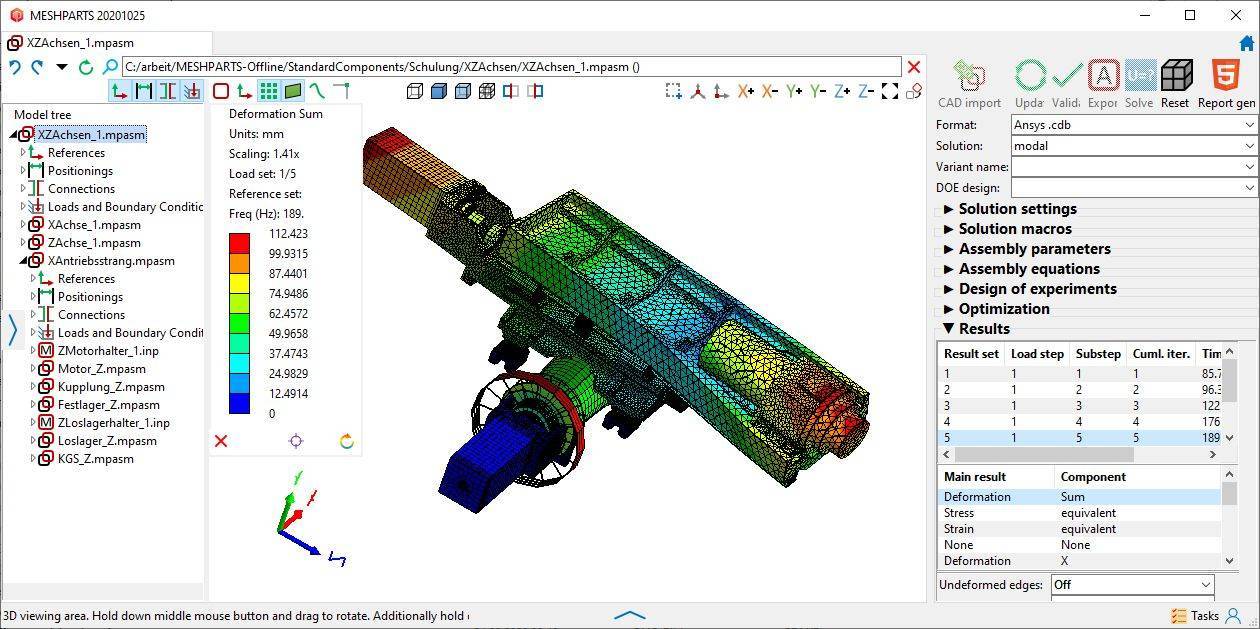